URSULA: Underwater Robotics
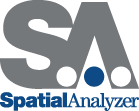
URSULA: Underwater Robotics
The URSULA Manipulator was designed and developed by Framatome-ANP (Advanced Nuclear Power) in Lynchburg, VA.
Project Overview
URSULA is an underwater robotic inspection system designed to inspect the welds in the reactor of a nuclear power plant. The manipulator weights approximately 900 lbs and locks on the reactor vessel using three suction cups on its base. In order to move around the vessel wall, URSULA exchanges its scanning head for a suction cup tool, unlatches the base and relocates using the arm with the tool locked to the wall.
This 6 degree of freedom manipulator uses special harmonic-drive submersible joints to provide high-torque, low-speed motion. An ultra sonic scanning head is mounted to the end-effector and used to scan the welds throughout the reactor.
NRK Involvement
New River Kinematics (NRK) provided several code modules critical to the operation of the URSULA system.
Robust Inverse Kinematics and Path Planning: Due to the scanning requirements, much of URSULA's motion requires navigating near and through singularities in the kinematic workspace of the robot. In the above figure, a sample scan patch is shown along with a red indicator for the region that was not navigable with standard inverse kinematics and path planning.
NRK used the robust inverse kinematics and path planning module from the RobotAssist product to replace the original kinematics and path planning modules in URSULA. The result was a dramatic improvement in useable workspace due to successful navigation of singularities in the workspace.
Real-Time Conversion of Joint Values to Scan-Patch UV Coordinates: The UT scan data is gathered as the manipulator scans across a weld area. In order to correlate the UT data with the exact scanner position within the reactor, it is necessary to compute the scan-patch coordinates (u,v) in real-time and mark the UT data accordingly.
NRK developed an efficient forward kinematic engine capable of dealing with the data at an extremely high rate. This module also converted the tool transformation of the manipulator to scan-patch UV coordinate values.
Underwater Laser GPS: Since URSULA is capable of walking around within the reactor, it is necessary to determine the transformation of its base within the reactor vessel. To do this, Framatome-ANP developed an underwater camera and laser system that projected a laser beam to a series of detectors on the base of the manipulator. Once centered on the receivers, the complete base transformation of the manipulator is computed.
NRK developed the optimization algorithms capable of combining several sources of data to compute the base transformation of the robot. These information sources included the angular information from the laser pointer, inclinometer values from the robot base, and the fact that the robot was positioned with its suction feet touching a cylindrical surface.
Using this combined data approach to solving for the robot base transformation, NRK was able to accurately determine URSULA's position within the reactor environment.
Click here to learn more about our custom applications or click here to read more about real-world SA applications.